The world of prosthetics is changing rapidly, and 3D printing is at the heart of this transformation. Traditional prosthetic limbs have long been expensive and time-consuming to produce, often limiting access for those in need. Now, 3D-printed prosthetics are breaking down these barriers, offering affordable, customizable, and efficient solutions that are reshaping how we think about limb replacement.
This article explores the exciting possibilities of 3D-printed prosthetics, detailing their benefits, the technology behind them, and what makes them a revolutionary choice for users and the industry alike. Let’s uncover how this innovation is creating new opportunities and paving the way for a more inclusive future.
How 3D Printing is Transforming Prosthetics
At its core, 3D printing, also known as additive manufacturing, involves creating objects layer by layer from digital models. In prosthetics, this technology allows for precise designs tailored to each user’s unique anatomy, lifestyle, and preferences. The result is a prosthetic that feels more natural, fits better, and performs more effectively than conventional options.
Speeding Up Production
One of the most significant advantages of 3D printing is its speed. Traditional prosthetics often require weeks or even months to manufacture, as they involve complex processes and multiple stages. In contrast, a 3D-printed prosthetic can be produced in a matter of days, drastically reducing wait times for users.
This rapid production also benefits healthcare providers and businesses. By cutting down on delays, manufacturers can serve more clients efficiently, ensuring that no one is left waiting for the solution they need.
At Robobionics, we leverage this capability to deliver high-quality prosthetics without sacrificing speed or precision.
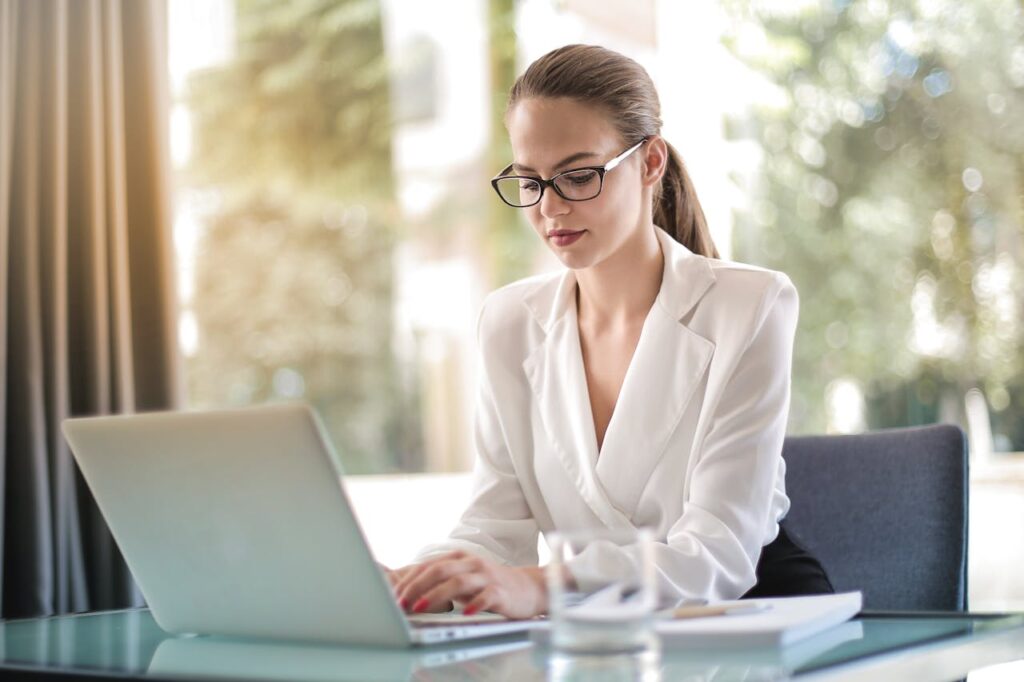
Making Prosthetics Affordable
Cost has long been a barrier in prosthetic care. Advanced features and durable materials drive up the price of traditional prosthetics, putting them out of reach for many individuals. 3D printing addresses this challenge by using cost-effective materials and streamlining production.
The affordability of 3D-printed prosthetics doesn’t mean compromising on quality. Lightweight, durable materials like PLA or PETG are commonly used, offering strength and comfort comparable to traditional options.
This affordability opens the door for more people to access life-changing prosthetic solutions, particularly in low-income and underserved communities.
Streamlining the Manufacturing Process
One of the most profound impacts of 3D printing is its ability to streamline production workflows. Unlike traditional manufacturing, which often involves multiple stages of tooling, molding, and assembly, 3D printing consolidates these processes into a single, seamless operation.
By working directly from digital models, manufacturers can eliminate the need for intermediate steps, significantly reducing production times and labor costs.
For businesses, this efficiency translates to increased scalability. Smaller operations can handle higher volumes without the need for extensive infrastructure, while larger organizations can focus on reducing lead times and serving more clients simultaneously.
By investing in high-capacity 3D printers and automation systems, companies can position themselves as reliable and responsive providers in an increasingly competitive market.
Democratizing Access to Prosthetics
Traditional prosthetics manufacturing often involves specialized facilities and costly equipment, creating accessibility gaps for individuals in remote or underserved regions. 3D printing, however, decentralizes production.
Prosthetics can now be designed in one location and printed in another, allowing providers to deliver solutions directly to areas with limited access to advanced healthcare facilities.
This decentralization creates opportunities for businesses to expand their reach. Partnering with local clinics, NGOs, or community health initiatives can help bridge the gap between advanced prosthetic technology and populations that need it most.
Establishing mobile 3D printing units or localized production hubs further enhances accessibility, building trust and loyalty in emerging markets.
Empowering Rapid Prototyping and Innovation
Innovation in prosthetics thrives on the ability to test and refine designs quickly. With 3D printing, rapid prototyping has become a cornerstone of the design process. New ideas can be brought to life, evaluated, and iterated upon in a fraction of the time it would take with traditional methods.
For businesses, this agility fosters a culture of experimentation and creativity. Prosthetics can be tailored to specific user needs, whether it’s optimizing for comfort, performance, or aesthetics. Collaborating with users during the prototyping phase ensures the final product aligns closely with their expectations.
Providers that adopt an iterative approach to design gain a significant edge, delivering prosthetics that are not only innovative but also deeply personalized.
Enhancing Environmental Sustainability
Sustainability has become a central focus for industries worldwide, and 3D printing aligns perfectly with these goals. By using additive manufacturing techniques, 3D printing minimizes material waste.
Unlike traditional methods that often involve cutting or carving from larger blocks of material, 3D printing builds the prosthetic layer by layer, using only what is necessary.
For businesses, integrating sustainability into their operations is both a practical and ethical imperative. Highlighting the environmental benefits of 3D-printed prosthetics in marketing and outreach efforts can resonate with eco-conscious users and stakeholders.
Additionally, exploring recyclable materials or bioplastics as printing substrates further reinforces a commitment to green practices, enhancing brand reputation and appeal.
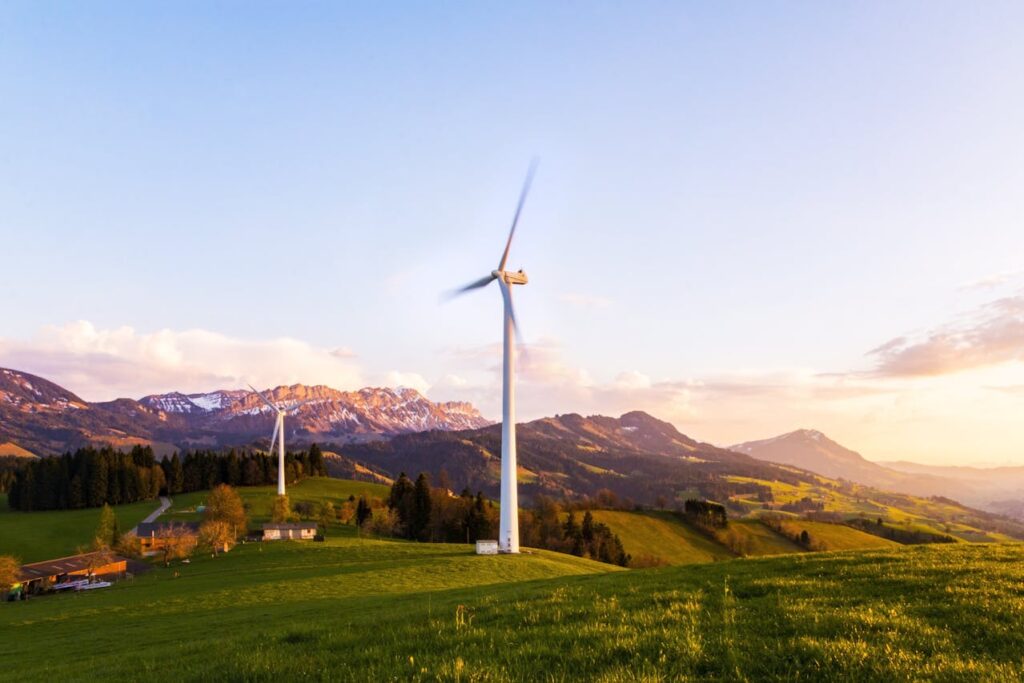
Bridging the Gap Between Affordability and Advanced Features
Historically, affordability and advanced functionality in prosthetics have been at odds. High-tech prosthetics with features like microprocessors or energy-return feet often come with prohibitive price tags, limiting their accessibility.
3D printing is closing this gap by significantly lowering production costs while enabling the integration of sophisticated components.
For businesses, this balance between cost and capability opens new avenues for product development. Offering customizable add-ons or tiered feature sets allows users to select options that align with their budget and lifestyle.
Providing modular solutions, where advanced components can be added over time, ensures that users have access to high-performance prosthetics without requiring an upfront investment in premium models.
Strengthening Supply Chain Resilience
The COVID-19 pandemic highlighted vulnerabilities in global supply chains, particularly for industries reliant on complex manufacturing processes. 3D printing addresses these challenges by enabling on-demand production. Materials can be sourced locally, and prosthetics can be manufactured closer to end-users, reducing dependency on international logistics.
For businesses, this resilience is a strategic advantage. Establishing decentralized printing networks or maintaining an inventory of digital designs ready for production ensures continuity in the face of disruptions.
Additionally, offering digital consultations and remote design services enhances flexibility, allowing businesses to adapt quickly to changing circumstances and user needs.
The Benefits of Customization
Customization is where 3D-printed prosthetics truly shine. Each prosthetic is designed based on detailed scans of the user’s residual limb, ensuring a fit that is not only comfortable but also optimized for functionality.
This personalized approach minimizes the risk of discomfort, pressure sores, or misalignment that can occur with generic or ill-fitting devices.
Tailored to Individual Needs
3D printing allows for unparalleled flexibility in design. For instance, a child’s prosthetic can include playful, colorful elements, while an adult’s prosthetic might focus on sleek, professional aesthetics.
Beyond appearance, functionality can also be tailored. Users with active lifestyles can benefit from enhanced strength and mobility features, while those with specific needs, such as typing or fine motor tasks, can opt for designs that support these activities.
At Robobionics, we work closely with users to understand their unique goals and preferences, translating them into customized prosthetic designs that meet both their practical and personal needs.
Encouraging Innovation and Experimentation
Because 3D printing is relatively quick and cost-effective, it encourages experimentation. Prototypes can be produced, tested, and refined in a short period, allowing designers to push the boundaries of what prosthetics can achieve.
This iterative process fosters innovation, leading to solutions that are not only functional but also highly user-centric.
For businesses, embracing 3D printing as a creative tool rather than just a manufacturing method can unlock new possibilities. Offering users the opportunity to collaborate on their prosthetic designs creates a sense of ownership and pride, further enhancing their experience.
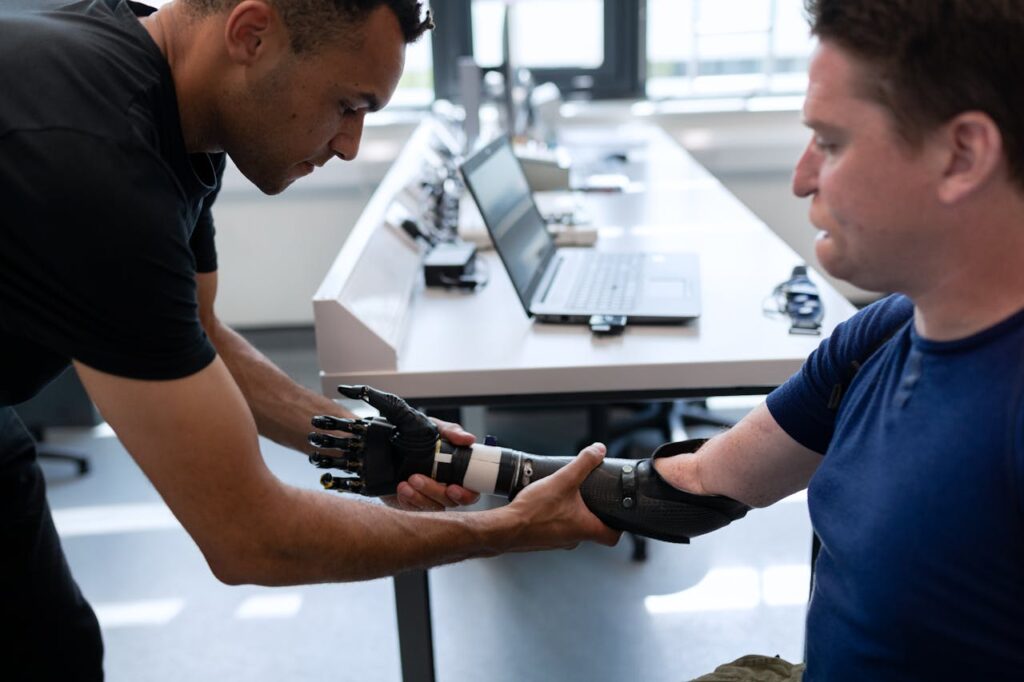
Advanced Technology in 3D-Printed Prosthetics
The rapid evolution of technology is pushing the capabilities of 3D-printed prosthetics to new heights. From incorporating sensors and smart components to leveraging AI and IoT for enhanced functionality, these advancements are transforming prosthetics into intelligent devices that go beyond traditional expectations.
Integrating Sensors for Real-Time Feedback
One of the most promising developments in 3D-printed prosthetics is the integration of sensors. These tiny devices can detect pressure, motion, and even temperature, providing users with valuable real-time feedback.
For example, a 3D-printed hand prosthetic equipped with tactile sensors could alert the user if they’re applying too much force when gripping an object.
Sensors can also enhance safety and comfort. By monitoring pressure points within the socket, the prosthetic can help prevent discomfort or injury caused by prolonged use.
For businesses, integrating sensors into 3D-printed designs represents a major leap forward in delivering prosthetics that are not only functional but also intuitive and user-friendly.
Incorporating Artificial Intelligence
Artificial intelligence (AI) is enabling smarter, more adaptive prosthetics. AI algorithms can analyze a user’s movements and predict their next actions, allowing the prosthetic to respond faster and more naturally.
In a 3D-printed prosthetic, these capabilities can be embedded seamlessly, offering advanced functionality at a fraction of the cost of traditional high-tech options.
For instance, a leg prosthetic could use AI to optimize walking efficiency, reducing energy expenditure for the user. Businesses investing in AI-enhanced 3D-printed prosthetics can set themselves apart as innovators in a highly competitive field.
Leveraging IoT for Connectivity
The Internet of Things (IoT) is another game-changer for 3D-printed prosthetics. IoT-enabled prosthetics can connect to apps, wearables, or healthcare systems, allowing users to track their activity, monitor performance, or receive remote support.
This connectivity creates a holistic user experience, where the prosthetic becomes part of a broader ecosystem of care.
For businesses, offering IoT features can improve user satisfaction and open opportunities for ongoing engagement. Apps that sync with prosthetics to provide tips, maintenance reminders, or updates ensure that users remain connected to their provider, building trust and loyalty.
Addressing Challenges in 3D-Printed Prosthetics
While 3D-printed prosthetics hold immense promise, they are not without challenges. For businesses and users alike, understanding and addressing these hurdles is key to maximizing the potential of this technology.
Material Limitations
Though 3D printing offers access to affordable materials, not all are suitable for prosthetics. Durability, weight, and biocompatibility are critical factors, and finding materials that strike the right balance can be challenging.
Advanced materials like carbon-reinforced polymers or medical-grade composites are emerging solutions, offering the strength and flexibility required for everyday and high-performance use.
For businesses, investing in research to identify and test new materials ensures that their 3D-printed prosthetics meet the highest standards of safety and functionality. Collaborating with material scientists or additive manufacturing experts can accelerate this process.
Scaling Production
As demand for 3D-printed prosthetics grows, scaling production while maintaining quality is a significant challenge. Unlike traditional manufacturing, where processes are standardized, 3D printing often involves a high degree of customization.
Balancing efficiency with personalization requires robust workflows and advanced printing technologies.
Businesses can address this by adopting modular design strategies, where components are standardized but tailored during final assembly. Implementing automated quality control measures, such as AI-driven inspections, ensures consistency without compromising on individuality.
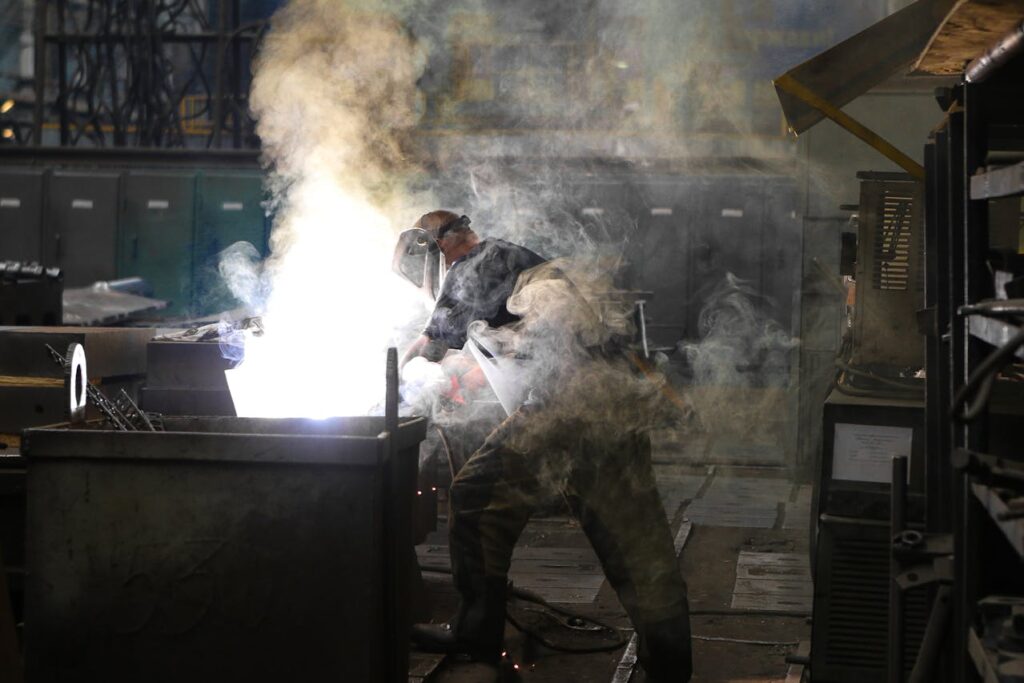
Training and Education
For users, adapting to a 3D-printed prosthetic may require education and training, especially if it includes advanced features like sensors or connectivity.
Similarly, healthcare providers and prosthetists must stay up to date with the latest 3D printing techniques and capabilities to offer effective guidance.
Businesses that provide comprehensive training programs, both for users and professionals, can bridge this gap. Interactive tutorials, workshops, and online resources help ensure that everyone involved is equipped to maximize the benefits of 3D-printed prosthetics.
How Businesses Can Embrace the 3D-Printing Revolution
For companies in the prosthetics industry, adopting 3D printing is no longer optional—it’s essential to staying competitive in a rapidly evolving market. Embracing this technology requires a strategic approach that focuses on innovation, collaboration, and user satisfaction.
Cultivating Partnerships
Collaboration is key to success in 3D printing. Partnering with tech firms, material suppliers, or academic institutions can provide access to cutting-edge tools and expertise. These partnerships accelerate innovation, allowing businesses to deliver state-of-the-art prosthetics that meet user demands.
At Robobionics, we actively collaborate with researchers and industry leaders to push the boundaries of what 3D-printed prosthetics can achieve. By combining our expertise with insights from diverse fields, we create solutions that are both practical and visionary.
Prioritizing Accessibility
One of the greatest strengths of 3D printing is its potential to make prosthetics accessible to underserved populations. Businesses should prioritize affordability and explore models that cater to users with limited resources.
Offering tiered pricing, localized production, or simplified designs can expand access and create a meaningful impact.
Empowering Users Through 3D-Printed Prosthetics
The success of any prosthetic, including those made using 3D printing, depends on how well it integrates into the user’s life. Beyond the technology and design, empowering users to embrace their prosthetic and maximize its potential is critical.
Businesses must focus on creating solutions that not only address mobility challenges but also inspire confidence, independence, and pride in the device.
Enhancing Personalization
3D-printed prosthetics allow for an unprecedented level of personalization, giving users the opportunity to take ownership of their device.
Whether it’s incorporating unique colors, patterns, or even functional enhancements tailored to hobbies and professions, personalization makes the prosthetic feel like an extension of the user’s identity.
For businesses, fostering this connection can be a powerful differentiator. Providing tools or platforms that let users co-create their designs enhances engagement and satisfaction.
At Robobionics, we actively involve users in the design process, ensuring that each prosthetic reflects their personality, preferences, and goals.
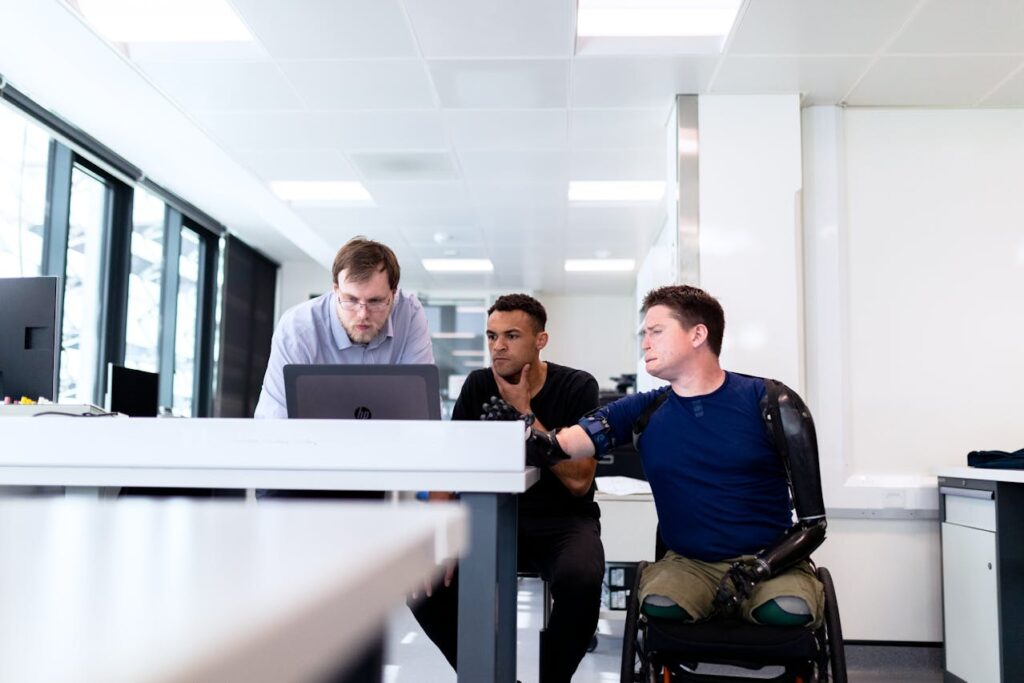
Building Confidence Through Training
Adapting to a new prosthetic can be daunting, especially for first-time users. Training plays a crucial role in building confidence and ensuring smooth integration into daily life.
For 3D-printed prosthetics, which may include innovative features like smart sensors or energy-return components, targeted training programs are essential.
Interactive tutorials, gamified exercises, and one-on-one support help users familiarize themselves with their device while making the process enjoyable.
Businesses that prioritize comprehensive training not only improve user outcomes but also strengthen their reputation as trusted providers.
Future Trends in 3D-Printed Prosthetics
The future of 3D-printed prosthetics is bright, with advancements in technology, materials, and design driving continuous innovation. These trends promise to make prosthetics more intuitive, accessible, and life-changing than ever before.
Bioprinting for Seamless Integration
Bioprinting, a cutting-edge development in additive manufacturing, involves creating structures that mimic biological tissues. In prosthetics, this could enable the production of prosthetic sockets that integrate more naturally with the user’s residual limb, reducing discomfort and improving stability.
For businesses, exploring bioprinting opens new possibilities for creating devices that feel like a natural part of the body. As this technology matures, companies that invest early will be well-positioned to lead the next generation of prosthetic solutions.
Smarter, More Adaptive Devices
The integration of AI and machine learning in 3D-printed prosthetics is set to redefine user experience. These technologies enable prosthetics to learn from a user’s movements and adapt to their unique patterns over time.
For example, a hand prosthetic could adjust its grip strength automatically based on the weight of an object.
For businesses, incorporating smart capabilities into 3D-printed designs is an opportunity to deliver products that are not just functional but transformative. Regular updates and feature enhancements can also create a long-term relationship between the provider and the user.
Advancing Material Science for Enhanced Performance
Material innovation will play a pivotal role in shaping the next generation of 3D-printed prosthetics. Research is focused on developing materials that replicate the properties of natural limbs, such as flexibility, resilience, and the ability to withstand diverse environmental conditions.
Smart materials, which change their properties in response to external stimuli like temperature or pressure, are set to revolutionize prosthetics, offering users adaptive and more life-like experiences.
For businesses, investing in partnerships with material scientists and suppliers is a strategic move. By being early adopters of cutting-edge materials, companies can offer prosthetics that set them apart in terms of comfort, durability, and performance. Marketing these innovations as user-focused enhancements positions brands as leaders in the field.
AI-Powered Predictive Customization
Artificial intelligence (AI) is paving the way for hyper-customization in prosthetics. By analyzing data from users’ movements, muscle patterns, and activity levels, AI can predict what adjustments or features would enhance functionality. This capability allows manufacturers to design prosthetics that are not only personalized but also adaptive over time.
For businesses, integrating AI into the design and post-delivery phases provides a unique selling point. Offering solutions that improve with use builds trust and enhances user satisfaction.
Companies can also use AI-generated insights to refine product development, ensuring that their prosthetics consistently address real-world user needs.
Collaborative Robotics in Fabrication
Robotics is set to enhance the precision and efficiency of 3D printing processes, enabling the creation of more complex and intricate prosthetic designs.
Collaborative robots, or cobots, can work alongside human designers to execute tasks like multi-material printing and real-time quality control. This integration of robotics streamlines production while maintaining the flexibility required for customization.
Businesses adopting robotic technologies in their manufacturing workflows can significantly improve scalability and consistency. Highlighting the role of robotics in creating high-quality, affordable prosthetics can also enhance a brand’s image as a tech-savvy and reliable provider.
Virtual Reality in User Experience Design
Virtual reality (VR) is emerging as a powerful tool for enhancing both the design and adoption of 3D-printed prosthetics. By immersing users in a virtual environment, they can visualize and interact with prosthetic designs before production begins.
This approach minimizes misunderstandings and ensures that the final product aligns closely with user expectations.
For businesses, integrating VR into the customer journey adds a layer of transparency and engagement. Offering virtual fittings or design consultations can improve user confidence and satisfaction, fostering stronger relationships between providers and clients.
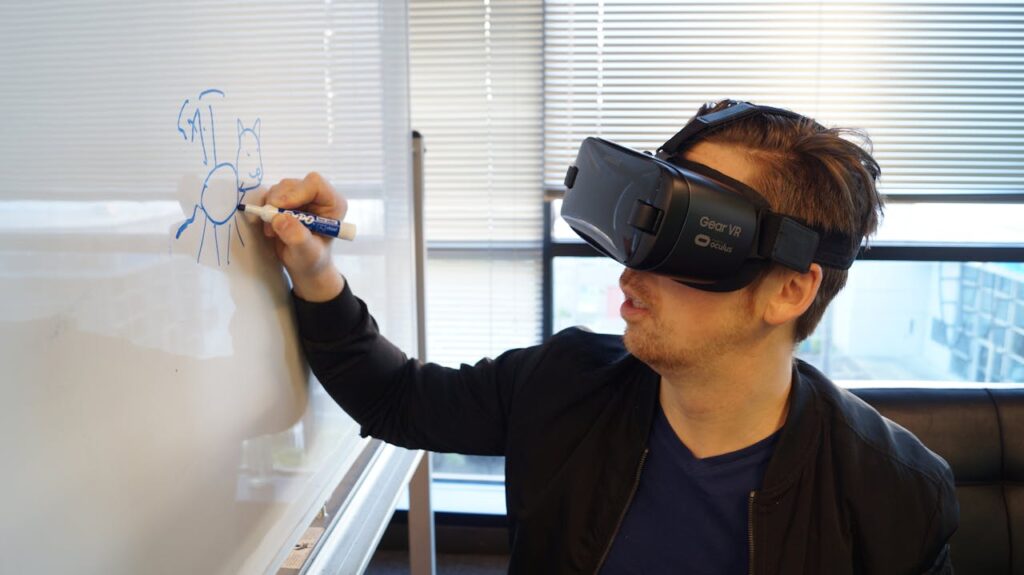
Decentralized Production Models
As 3D printing technology becomes more accessible, the industry is moving toward decentralized production. Prosthetics can be manufactured closer to end-users, reducing transportation costs and lead times.
This model is particularly beneficial for underserved regions, where access to advanced prosthetic solutions has historically been limited.
Businesses embracing decentralized production can establish a presence in emerging markets and expand their reach. Partnering with local clinics or setting up regional printing hubs ensures that users receive timely and cost-effective solutions.
This approach not only boosts accessibility but also strengthens brand loyalty by demonstrating a commitment to community impact.
Conclusion
3D-printed prosthetics are not just a technological innovation—they’re a revolution in accessibility, personalization, and functionality. By addressing long-standing barriers like cost and production times, 3D printing is empowering individuals with limb loss to live more independent, fulfilling lives.
For businesses, the opportunities are equally transformative. Embracing 3D printing allows companies to deliver cutting-edge solutions that are both affordable and impactful.
By focusing on user-centric design, advanced features, and holistic support, providers can lead the way in shaping a future where prosthetics are accessible to all.