Prosthetic technology has come a long way, evolving from heavy, mechanical limbs to lightweight, custom-fit, and highly functional artificial limbs. One of the biggest breakthroughs in the field is 3D printing, which has completely changed how prosthetics are designed, manufactured, and distributed.
With 3D printing, prosthetic limbs can be created faster, cheaper, and with greater personalization than ever before. This technology has made it possible for more people to access affordable, high-quality artificial limbs, eliminating many of the barriers that once existed. By 2030, 3D-printed prosthetics will be the norm, offering unmatched customization, comfort, and accessibility.
At Robobionics, we are committed to harnessing 3D printing technology to transform prosthetic design, ensuring that our users receive the best, most advanced solutions available. In this article, we explore how 3D printing is shaping the future of prosthetic design, making artificial limbs more efficient, cost-effective, and user-friendly.
1. How 3D Printing Has Changed Prosthetic Manufacturing
Before 3D printing, prosthetic manufacturing was a time-consuming and expensive process. Traditional prosthetics were made using casting, molding, and manual adjustments, requiring multiple clinic visits and long production times. Each prosthetic had to be crafted individually, making it difficult to mass-produce affordable options.
3D printing has eliminated these challenges by enabling on-demand prosthetic manufacturing. With digital scanning and 3D modeling, prosthetic limbs can be printed layer by layer in just a few hours. This process reduces waste, labor costs, and material expenses, making prosthetics more affordable and widely available.
By 2030, 3D printing will be the primary method for prosthetic production, ensuring that people around the world have quick and cost-effective access to custom-fit artificial limbs.
2. Customization: Tailoring Prosthetics to Each User’s Needs
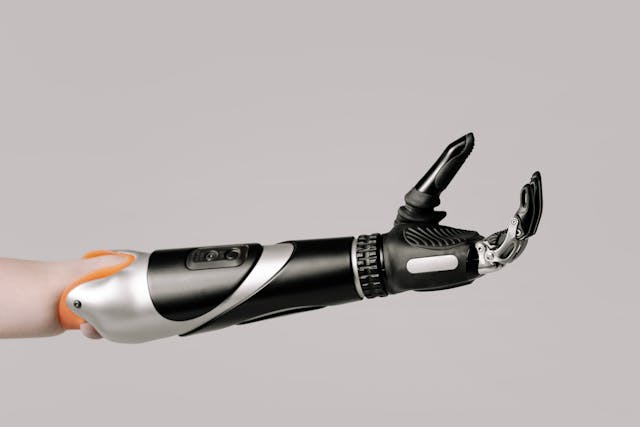
One of the biggest advantages of 3D-printed prosthetics is personalization. Every person’s body is different, and a prosthetic limb must be precisely designed to fit their unique shape, movement patterns, and lifestyle needs.
With 3D scanning technology, prosthetists can digitally map a user’s residual limb and create a custom-fit prosthetic design. This ensures a perfect fit with better comfort, improved mobility, and reduced risk of skin irritation or discomfort. Users can also choose specific colors, patterns, and finishes, making their prosthetic limb feel more personal and natural.
By 2030, custom-fit 3D-printed prosthetics will become the standard, giving users greater control over their artificial limbs and improving long-term wearability.
3. Making Prosthetics More Affordable with 3D Printing
One of the biggest barriers to prosthetic access is cost. Traditional prosthetic limbs can cost thousands of dollars, making them unaffordable for many people, especially in developing countries. 3D printing is dramatically reducing these costs, making high-quality prosthetic limbs available at a fraction of the price.
With low-cost materials like bioplastics and lightweight polymers, 3D-printed prosthetics are cheaper to produce without compromising on durability. Additionally, because 3D printers can create prosthetics in a matter of hours, production costs are significantly reduced.
By 2030, 3D-printed prosthetic limbs will cost up to 70% less than traditional models, ensuring that everyone, regardless of financial status, has access to mobility solutions.
4. Faster Production: Reducing Wait Times for Prosthetic Users
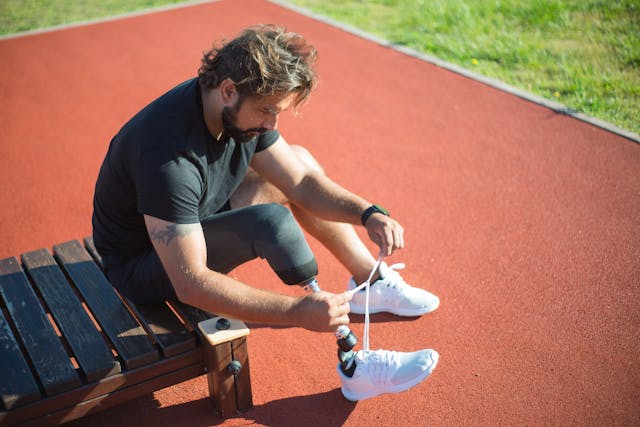
For many people, waiting weeks or months for a prosthetic limb can be frustrating and inconvenient. Traditional prosthetic manufacturing involves multiple steps, including molding, manual assembly, and fitting adjustments, which can slow down the process.
With 3D printing, prosthetic production is significantly faster. Once a digital model is created, a complete limb can be printed in just a few hours or days, depending on the complexity of the design. This means that users can receive their prosthetic devices much sooner, allowing them to regain mobility and independence faster.
By 2030, same-day or next-day prosthetic delivery will become common, ensuring that users never have to wait long for a replacement or new limb.
5. Lightweight and Durable Materials for Improved Comfort
Traditional prosthetics are often made from metal, fiberglass, or heavy plastics, which can be bulky and uncomfortable for long-term use. 3D printing has introduced new lightweight materials that offer better flexibility, comfort, and strength.
Modern biocompatible polymers, carbon fiber-reinforced plastics, and flexible resins are now being used to create prosthetic limbs that are lighter, stronger, and more natural to wear. These materials also improve shock absorption and movement range, reducing stress on joints and muscles.
By 2030, prosthetic limbs will be made from ultra-lightweight 3D-printed materials, ensuring that users experience maximum comfort and durability.
6. 3D Printing for Pediatric Prosthetics: Growing with the Child
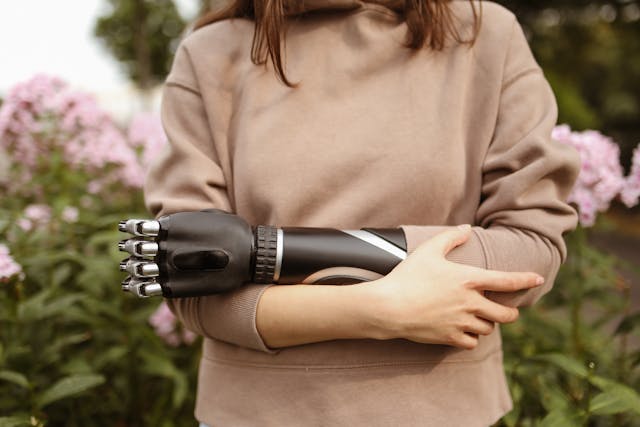
Children who need prosthetic limbs often require frequent replacements as they grow. Traditional prosthetic replacements can be expensive and time-consuming, making it difficult for families to afford regular adjustments.
With 3D printing, pediatric prosthetics can be easily resized and reprinted at a low cost. Instead of replacing an entire limb, only specific parts can be updated as the child grows. This ensures that children always have a comfortable, functional prosthetic without financial burden.
By 2030, 3D-printed pediatric prosthetics will become standard, allowing kids to grow with their prosthetics and stay active without limitations.
7. The Role of AI in 3D-Printed Prosthetic Design
Artificial Intelligence (AI) is improving how 3D-printed prosthetics are designed, customized, and optimized. AI-powered software can analyze a user’s movement patterns and automatically adjust prosthetic designs for better performance.
Machine learning algorithms can predict pressure points, suggest modifications, and refine joint flexibility, ensuring that each prosthetic is perfectly tailored to the user’s needs. AI can also automate the design process, reducing human error and making prosthetic customization faster and more precise.
By 2030, AI-assisted 3D printing will produce prosthetics that adapt to users’ movement habits, improving both functionality and comfort.
8. The Future of 3D-Printed Bionic Limbs
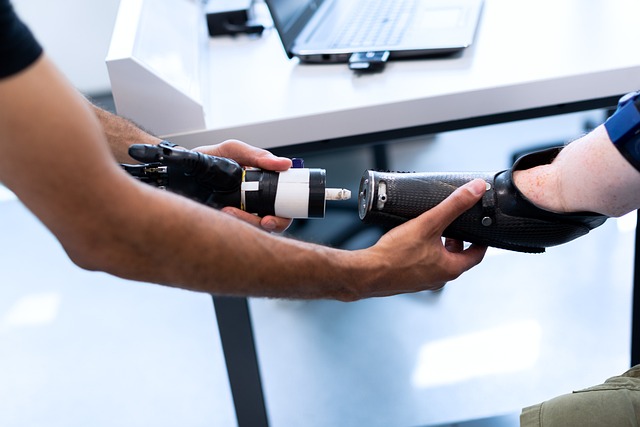
Bionic limbs with advanced sensors, robotic joints, and AI-driven movement are becoming more common, and 3D printing is making them more accessible.
Future 3D-printed prosthetics will include:
- Embedded sensors for real-time movement tracking
- Haptic feedback technology for touch sensation
- Brain-machine interfaces for mind-controlled movement
By 2030, 3D-printed bionic prosthetics will be fully integrated with smart technology, allowing users to experience natural movement and control like never before.
9. The Role of 3D Printing in Emergency and Disaster Relief Prosthetics
One of the most overlooked benefits of 3D-printed prosthetics is their role in disaster relief and emergency medical care. In situations where people lose limbs due to earthquakes, war, or accidents, access to prosthetic limbs is often limited, expensive, or completely unavailable.
With mobile 3D printing units, prosthetic limbs can be designed and printed on-site in a matter of hours, allowing amputees to receive immediate assistance. These portable 3D printing stations can be set up in war zones, refugee camps, and disaster-stricken areas, ensuring that even in extreme conditions, amputees regain mobility as quickly as possible.
By 2030, global organizations and NGOs will deploy 3D printing prosthetic stations in disaster-prone areas, ensuring that prosthetic technology reaches those who need it most, when they need it most.
10. Sustainable 3D-Printed Prosthetics: A Greener Future
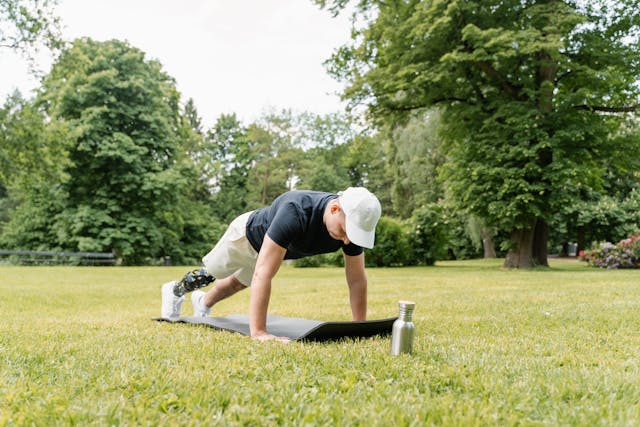
Traditional prosthetic production generates significant waste, as it often involves casting, molding, and machining, which leaves behind excess materials. Additionally, most prosthetics are made from non-biodegradable plastics and metals, which contribute to long-term waste.
3D printing is changing this by allowing prosthetic limbs to be made from sustainable, biodegradable, and recyclable materials. Innovations in bioplastics, bamboo composites, and algae-based polymers are making it possible to create eco-friendly prosthetic limbs that reduce environmental impact.
By 2030, sustainable 3D-printed prosthetics will be widely available, ensuring that mobility solutions are not only affordable and functional but also environmentally responsible.
11. Open-Source 3D Prosthetic Designs: Community-Driven Innovation
One of the most exciting trends in 3D-printed prosthetics is open-source collaboration. Engineers, designers, and healthcare professionals around the world are now sharing prosthetic designs online, allowing anyone with a 3D printer to create customized prosthetic limbs at a low cost.
Platforms like e-NABLE and Open Bionics have already demonstrated how crowdsourced innovation can make prosthetic technology more accessible. With open-source 3D designs, people in remote or underserved communities can download and print prosthetic limbs without needing access to expensive manufacturing facilities.
By 2030, open-source prosthetic technology will enable millions of people worldwide to receive high-quality, customized prosthetics, regardless of location or financial situation.
12. The Role of 3D Printing in Smart Prosthetics and Wearable Technology
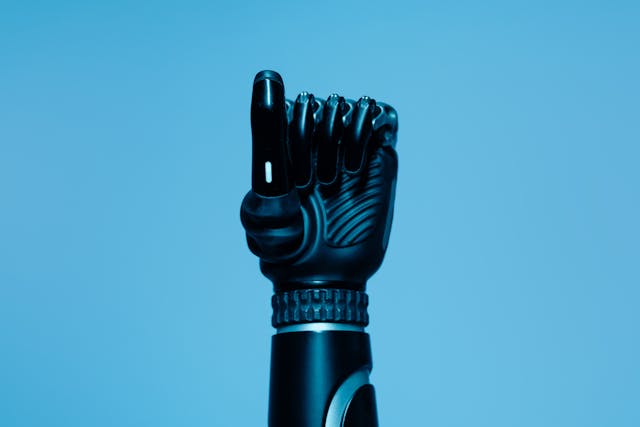
3D printing is not just about creating static prosthetic limbs—it’s also enabling the development of smart prosthetics that integrate with AI, IoT, and wearable technology.
In the future, 3D-printed smart prosthetics will:
- Connect to smartphones and fitness trackers, allowing users to monitor movement and health metrics.
- Automatically adjust fit and grip strength based on real-time AI learning models.
- Feature embedded sensors that provide haptic feedback, restoring a sense of touch.
By 2030, 3D-printed smart prosthetics will be fully integrated into wearable technology ecosystems, making them more interactive and user-friendly than ever before.
13. The Future of 3D Bioprinting: Prosthetics That Feel Like Real Limbs
While current 3D-printed prosthetics are primarily made from plastics and carbon fiber composites, future developments in 3D bioprinting could allow for the creation of prosthetic limbs that closely resemble biological tissue.
Scientists are already experimenting with 3D-printed muscle fibers, artificial skin, and even bioengineered nerves, which could eventually allow prosthetic users to regain sensation, temperature sensitivity, and even limited muscle function.
By 2030, bioengineered prosthetics will begin to bridge the gap between artificial and biological limbs, offering a more lifelike experience for amputees.
14. Personalized Fashion and Aesthetic Enhancements for 3D-Printed Prosthetics
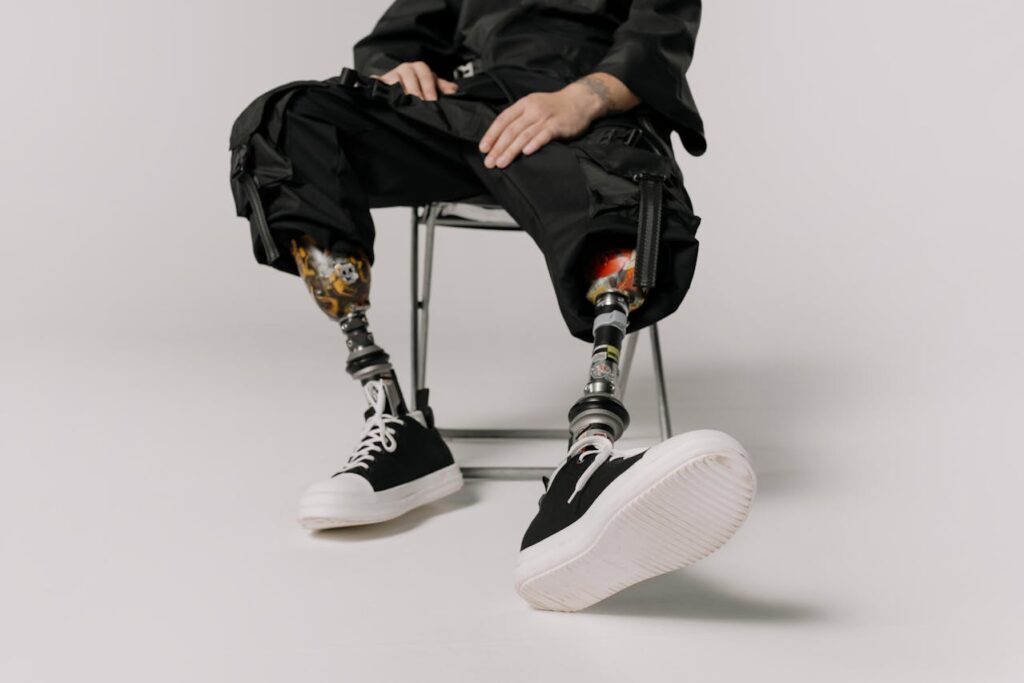
Prosthetic users are no longer limited to basic, skin-colored designs—3D printing is allowing for personalized, stylish prosthetic designs that reflect each user’s personality and preferences.
Future 3D-printed prosthetic limbs will allow users to:
- Choose from customizable designs, including geometric patterns, vibrant colors, and artistic engravings.
- Swap out prosthetic covers for different occasions, such as formal designs for work or LED-lit designs for special events.
- Incorporate functional add-ons, like built-in storage compartments or modular attachments for sports and hobbies.
By 2030, prosthetic limbs will no longer just be medical devices—they will be seen as fashion statements and personal expressions of identity.
15. How 3D Printing Will Make Prosthetics More Accessible in Rural Areas
One of the biggest challenges in prosthetic healthcare is accessibility in rural and remote regions, where prosthetic clinics are scarce. However, community-run 3D printing labs are emerging as a solution.
With affordable desktop 3D printers, local healthcare providers and even schools can manufacture prosthetic limbs within their own communities, reducing dependence on large-scale manufacturing facilities. Training programs are already being developed to teach local technicians and students how to 3D-print and assemble prosthetic limbs, empowering communities to become self-sufficient in prosthetic production.
By 2030, decentralized 3D printing labs will be available in rural clinics worldwide, ensuring that no one is left without mobility due to geographical limitations.
Final Thoughts: 3D Printing is the Future of Prosthetic Design
3D printing is revolutionizing prosthetic technology, making artificial limbs cheaper, faster, and more customizable than ever before. With lightweight materials, AI-driven design, and advanced customization, prosthetics are becoming more comfortable, functional, and accessible for users around the world.
At Robobionics, we are committed to leveraging 3D printing to create cutting-edge prosthetic solutions, ensuring that mobility is never limited by cost or accessibility.
If you’re ready to explore the future of 3D-printed prosthetic technology, book a free demo with Robobionics today and take the first step toward a more comfortable and personalized prosthetic experience!