The field of prosthetic arm technology is advancing rapidly, promising significant improvements in functionality and user experience between 2025 and 2030. These innovations aim to provide more natural movement, enhanced sensory feedback, and greater integration with the human body, transforming the lives of individuals with upper limb amputations.
Advanced Neural Interfaces for Intuitive Control
One of the most groundbreaking developments in prosthetic technology is the creation of direct brain-computer interfaces (BCIs). These systems allow users to control prosthetic arms using their thoughts, bypassing traditional muscle-based control methods. By implanting electrodes in the brain’s motor cortex, neural signals can be decoded and translated into precise movements of the prosthetic limb.
Direct Brain-Computer Interfaces
Recent studies have demonstrated the potential of BCIs in restoring motor functions. For instance, researchers at the University of Pittsburgh have developed brain-controlled robotic arms that enable users to perform complex tasks with high accuracy. This technology holds promise for providing amputees with a level of control and dexterity comparable to natural limbs.
As research progresses, BCIs are expected to become more refined, with less invasive implantation techniques and improved signal processing algorithms, making them a viable option for a broader range of users.
Muscle-Implantable Sensors
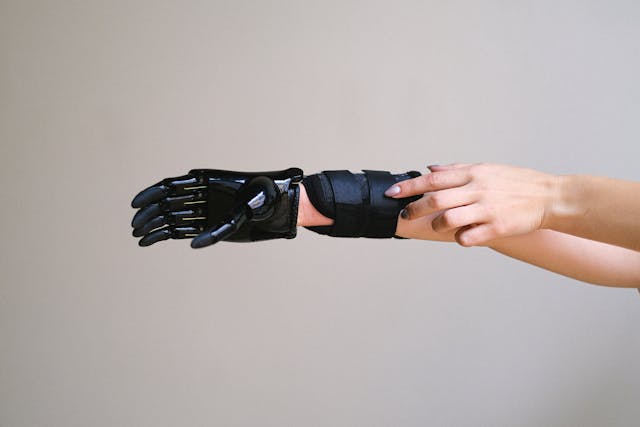
While BCIs offer direct neural control, less invasive alternatives are also being developed. Muscle-implantable sensors detect electrical signals from residual muscles in the amputated limb, translating them into movements of the prosthetic arm. This approach leverages existing neuromuscular pathways, allowing for intuitive control without the need for brain surgery.
Phantom Neuro, a startup company, is pioneering this technology by developing thin, flexible muscle implants that interface directly with the remaining muscles. In recent trials, participants successfully controlled robotic arms with high accuracy using these implants, performing a variety of hand and wrist gestures. This advancement suggests a future where amputees can achieve natural, thought-driven control of prosthetic limbs without invasive procedures.
The development of muscle-implantable sensors is poised to enhance the accessibility and functionality of prosthetic arms, offering a practical solution for many users.
Targeted Muscle Reinnervation
Targeted Muscle Reinnervation (TMR) is a surgical technique that reassigns nerves from amputated limbs to remaining muscles, allowing for more precise control of prosthetic devices. By connecting these nerves to specific muscle groups, users can generate distinct electrical signals corresponding to different movements, which are then detected by the prosthetic’s sensors.
This method has shown promising results in improving the intuitiveness and range of motions available to prosthetic arm users. As TMR techniques continue to evolve, they are expected to become more widely adopted, providing enhanced control options for individuals with upper limb amputations.
Sensory Feedback for Enhanced Perception
A significant challenge in prosthetic development has been the lack of sensory feedback, which is crucial for performing delicate tasks and achieving a sense of embodiment. Innovations are now focusing on integrating sensory feedback mechanisms that convey tactile information from the prosthetic hand to the user’s nervous system.
Restoring the Sense of Touch
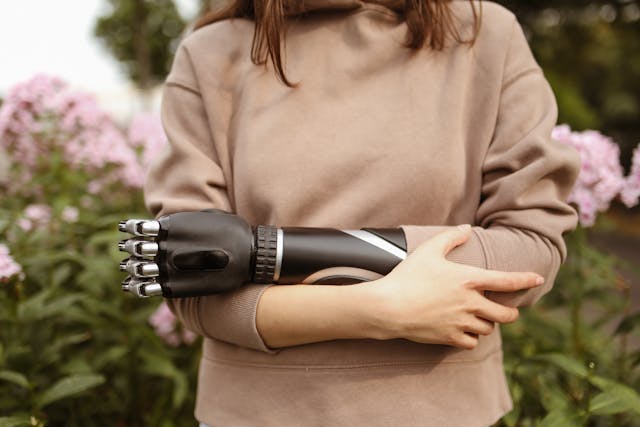
Researchers at the University of Chicago have made strides in this area by developing neurotechnological approaches that enable a realistic sense of touch in individuals using robotic hands controlled by brain signals. By implanting electrodes in the brain’s sensory regions, users can perceive tactile information such as edges, shapes, and movements, significantly enhancing their ability to interact with their environment.
This bidirectional communication between the brain and prosthetic devices is expected to become more sophisticated, offering users a more natural and functional experience.
Haptic Feedback Systems
In addition to direct neural integration, haptic feedback systems are being incorporated into prosthetic arms to simulate the sensation of touch. These systems use sensors on the prosthetic hand to detect pressure, texture, and temperature, relaying this information to the user through vibrations or electrical stimulation of the skin.
The LUKE Arm, developed by Mobius Bionics, exemplifies this approach by providing tactile feedback triggered by sensors in the thumb and other parts of the hand. Users can experience sensations that mimic natural touch, improving their ability to perform tasks that require fine motor skills.
As haptic technology advances, these systems are expected to offer more nuanced and varied sensations, further enhancing the functionality of prosthetic limbs.
Proprioceptive Feedback
Beyond tactile sensations, proprioception—the sense of the relative positioning of body parts—is essential for coordinated movement. Innovations are underway to provide prosthetic users with proprioceptive feedback, enabling them to sense the position and movement of their artificial limbs without visual cues.
This can be achieved through sensory substitution techniques, where information about limb position is conveyed through alternative sensory channels, such as auditory or visual feedback. Developing effective proprioceptive feedback systems will enhance the user’s ability to perform complex, coordinated movements with their prosthetic arms.
Advanced Materials and Manufacturing Techniques
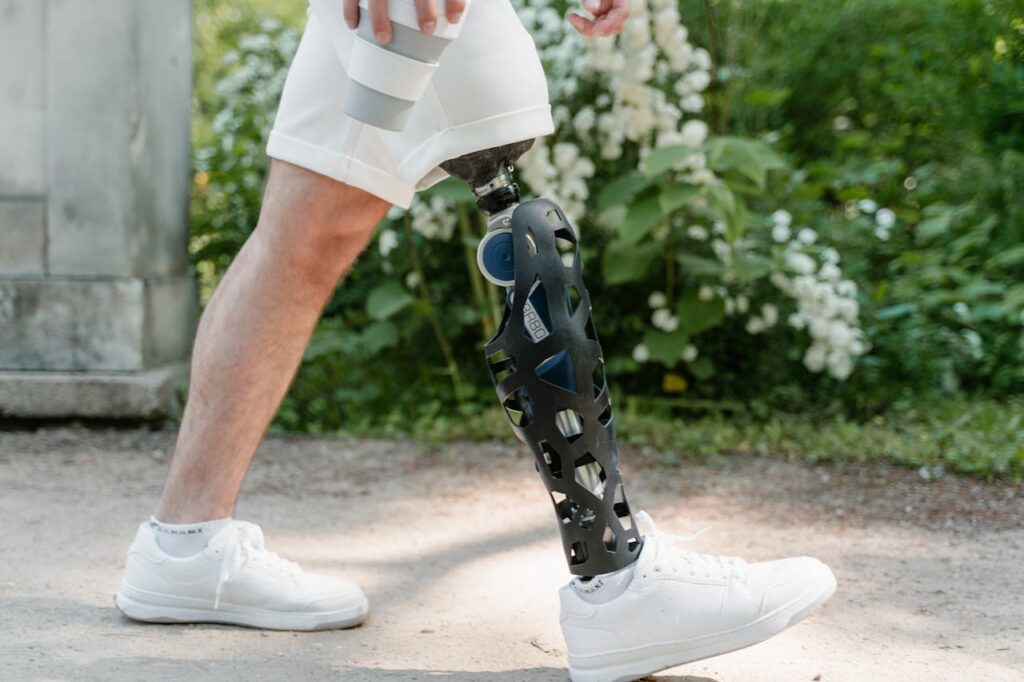
The advent of 3D printing technology has revolutionized the production of prosthetic limbs, allowing for rapid and cost-effective customization. By creating prosthetics tailored to the exact measurements and preferences of the user, 3D printing ensures a comfortable fit and personalized aesthetics.
3D Printing for Customization
Companies like Open Bionics have harnessed this technology to produce the Hero Arm, a lightweight, affordable bionic arm that can be customized with various designs. This approach not only improves functionality but also empowers users by allowing them to choose designs that reflect their personalities.
As 3D printing technology continues to advance, it is expected to further reduce production costs and time, making high-quality prosthetic arms more accessible to a broader population.
Lightweight and Durable Materials
The selection of materials plays a crucial role in the comfort and usability of prosthetic arms. Innovations in material science are leading to the development of prosthetics that are both lightweight and durable, reducing user fatigue and enhancing the range of motion.
arm. These sensors provide a more natural and intuitive control system, bridging the gap between traditional myoelectric prosthetics and fully brain-controlled limbs.
By implanting small, biocompatible sensors within the muscle tissue, these systems can pick up even the slightest muscle contractions. This allows users to execute precise hand and finger movements without relying on external electrodes. Unlike traditional myoelectric control, these implants offer better signal stability and faster response times, ensuring smoother motion.
As the technology progresses, we can expect wireless muscle implants that seamlessly communicate with prosthetic arms, eliminating the need for surface electrodes. This advancement will improve comfort, accuracy, and long-term wearability, making prosthetic control feel more natural than ever before.
AI-Powered Adaptive Learning Systems
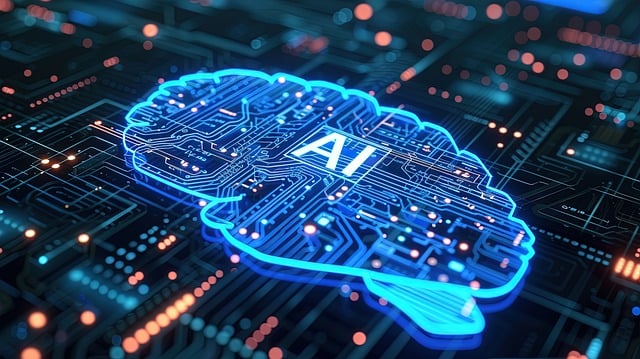
Artificial intelligence is set to revolutionize prosthetic arm functionality. AI-powered systems will learn from the user’s movement patterns, refining their responses over time for a more personalized experience. These systems will adjust grip strength, movement speed, and joint flexibility based on daily activities.
A user who frequently types on a keyboard will experience enhanced finger precision, while someone engaged in sports will benefit from faster, stronger grip adjustments. Over time, the prosthetic will adapt like a natural extension of the body, requiring less conscious effort from the user.
Future AI-driven prosthetics will also feature predictive movement technology, allowing the limb to anticipate the user’s intent. This will make multi-step actions—such as picking up a cup and bringing it to the mouth—more fluid and seamless, reducing cognitive load on the user.
Sensory Feedback and Tactile Perception
One of the most significant limitations of traditional prosthetic arms is the lack of sensory feedback. Without feeling texture, pressure, or temperature, users must rely on visual cues to gauge grip strength and object stability. Future prosthetic arms will integrate advanced sensory feedback systems that restore the sensation of touch.
Restoring the Sense of Touch
Researchers are developing electronic skin (e-skin) that mimics human skin’s ability to detect pressure, vibration, and texture. This ultra-thin material will be embedded in the prosthetic hand, allowing users to feel the softness of fabric, the firmness of a handshake, or the weight of an object.
By connecting e-skin to nerve stimulation implants, users will experience real-time touch sensations, making their interactions more natural and intuitive. This innovation will dramatically improve precision control, reducing accidental drops and enhancing fine motor skills.
Temperature Sensation and Realistic Textures
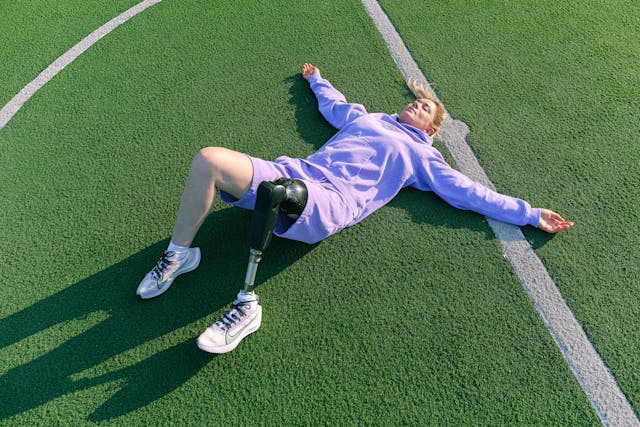
Beyond touch, the next generation of prosthetic arms will feature temperature sensors, allowing users to feel heat and cold. This will be particularly useful for daily activities like cooking, handling beverages, or interacting with the environment.
Advanced materials will also mimic the texture of human skin, improving the appearance and feel of prosthetic limbs. These synthetic skins will be stretchable, durable, and capable of self-repair, providing users with a more lifelike experience.
With these developments, prosthetic users will no longer experience a complete disconnect from their environment. Instead, they will be able to engage in daily tasks with greater confidence and precision, making prosthetic arms feel less like tools and more like natural limbs.
Nerve-Integrated Feedback Systems
The future of sensory feedback lies in direct nerve integration, where electrodes implanted in the user’s residual limb stimulate sensory nerves to recreate natural touch sensations. Unlike traditional vibration-based feedback, this method enables users to distinguish between different textures, grip pressures, and even pain levels.
Several research teams have successfully tested nerve-integrated prosthetic arms, with users reporting that they could identify objects without looking at them. By 2030, this technology will likely be refined to provide high-resolution sensory feedback, restoring near-natural touch perception.
Enhanced Dexterity and Multi-Grip Functionality
Modern prosthetic arms already feature basic grip modes, such as open-palm, pinch, and fist grips. However, next-generation prosthetics will introduce dynamic, multi-grip functionality, enabling users to seamlessly switch between different hand postures based on real-time activity needs.
Advanced Multi-Grip Control
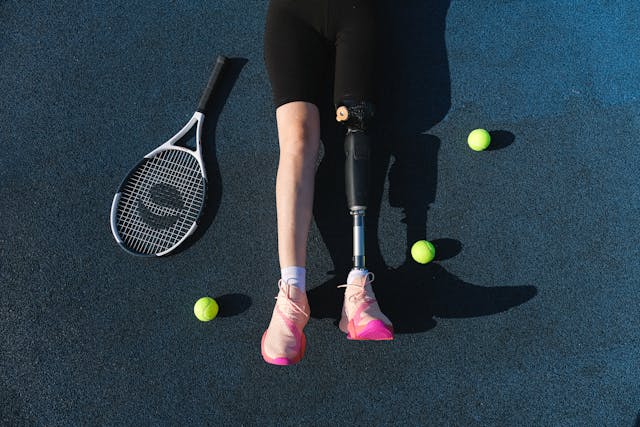
By integrating machine learning algorithms, these prosthetics will recognize patterns of movement and automatically adjust grip settings. For example, if a user frequently switches between typing and holding objects, the prosthetic will optimize hand positioning without requiring manual adjustments.
Future prosthetics will also allow users to perform complex finger movements, such as playing musical instruments, tying shoelaces, or handling delicate objects. These advancements will ensure that users can engage in a wider range of activities without limitations.
Rotational Wrist and Joint Flexibility
Another highly anticipated development is rotational wrist technology, which will allow users to twist and rotate their wrists naturally. Traditional prosthetic arms often have limited rotational movement, making certain tasks—like turning a doorknob or flipping a book page—more challenging.
By incorporating advanced actuators and micro-motors, future prosthetic arms will offer greater flexibility and natural joint movement. Some prototypes are already testing 360-degree wrist rotation, providing users with full freedom of movement.
These improvements will ensure that prosthetic arms function more like human limbs, reducing the effort required for everyday tasks and improving overall usability.
Smart Adaptive Finger Control
One of the most exciting innovations in prosthetic arms is independent finger control, where each finger can move individually and with variable pressure. Current prosthetic hands rely on preset grip patterns, but future designs will allow for natural, unrestricted hand movement.
This advancement will be particularly beneficial for users who engage in detailed, dexterous tasks, such as artists, engineers, and surgeons. By mirroring the natural motion of human fingers, these prosthetic hands will significantly enhance precision, grip strength, and coordination.
The Role of Sustainable and Affordable Prosthetics
3D-Printed Custom Prosthetics
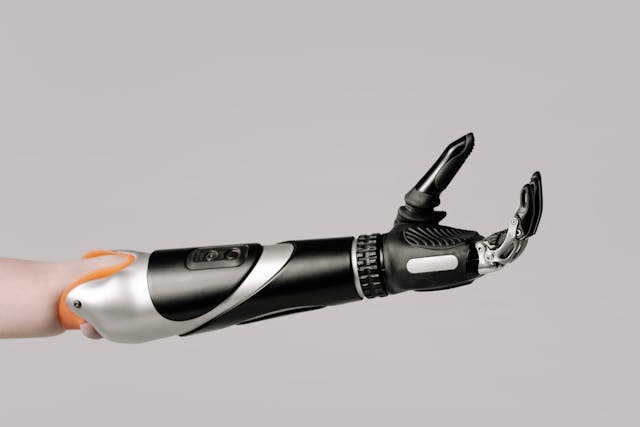
The rise of 3D printing technology is making prosthetic arms more accessible and cost-effective. By 2030, 3D-printed prosthetics will be widely available, allowing users to receive custom-fit limbs at a fraction of the cost of traditional models.
These prosthetic arms will be made from lightweight, durable materials, ensuring greater comfort and wearability. The ability to rapidly produce prosthetic limbs will also reduce waiting times, allowing users to receive quick replacements and upgrades as needed.
Modular and Upgradable Prosthetic Systems
Future prosthetic arms will feature modular designs, where users can swap out components based on their needs. Instead of purchasing an entirely new prosthetic, users will be able to upgrade specific parts, such as finger joints, wrist modules, or sensory feedback systems.
This approach will reduce costs, extend the lifespan of prosthetic arms, and allow for greater customization. As technology evolves, users can integrate new features into their existing prosthetics, ensuring they always have access to the latest advancements.
Biodegradable and Eco-Friendly Materials
Sustainability is becoming a major focus in prosthetic development. Scientists are exploring biodegradable materials and eco-friendly alternatives to traditional plastics and metals. Future prosthetics may be made from plant-based biopolymers, recycled composites, and self-repairing materials, reducing environmental impact while maintaining high durability and performance.
By 2030, sustainable prosthetic solutions will become more widely available, ensuring that cutting-edge prosthetic technology remains both environmentally responsible and affordable.
Final Thoughts: A New Era for Prosthetic Arms
Between 2025 and 2030, prosthetic arms will evolve beyond mechanical tools, becoming highly intelligent, sensory-rich, and seamlessly integrated with the human body.
With advancements in brain-controlled interfaces, AI-powered learning, sensory feedback, and sustainable materials, the future of prosthetic arms is set to redefine mobility, independence, and quality of life.
At Robobionics, we are committed to bringing these next-generation innovations to life. If you’re looking for a cutting-edge prosthetic solution, contact us today to explore the latest advancements in prosthetic arm technology.