The field of prosthetic design has undergone a dramatic transformation in recent years. What was once a static, mechanical solution is now evolving into a highly advanced, biomechanical integration of robotics, AI, and human physiology. With biomechanical engineering, prosthetic limbs are no longer just replacements for lost limbs—they are becoming intelligent, adaptive extensions of the human body.
Between 2025 and 2030, advancements in biomechanics, smart materials, neural interfaces, and AI-driven movement analysis are making prosthetic limbs more natural, efficient, and responsive. These breakthroughs are not only improving functionality but also enhancing comfort, durability, and sensory feedback for users.
At Robobionics, we are dedicated to pushing the boundaries of biomechanical engineering, ensuring that prosthetic users experience unmatched mobility, adaptability, and control. In this article, we explore how biomechanical engineering is reshaping prosthetic design, making artificial limbs smarter, stronger, and more human-like than ever before.
1. The Role of Biomechanical Engineering in Prosthetic Evolution
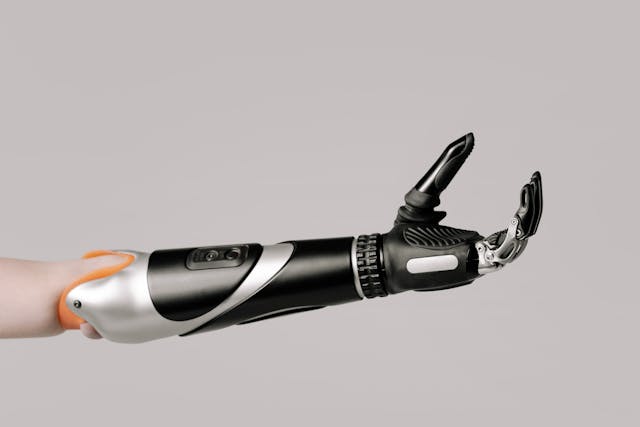
Biomechanical engineering is the science of merging biology with mechanical systems, allowing prosthetic limbs to replicate natural movement with extreme precision. This field combines robotics, material science, artificial intelligence, and human physiology to create prosthetic designs that are more functional and intuitive than ever before.
Unlike traditional prosthetics, which relied on mechanical hinges and rigid materials, modern biomechanical prosthetics are designed to mimic the structure and function of human muscles, tendons, and joints. Using hydraulic systems, soft robotics, and AI-driven motion sensors, these prosthetics allow fluid, natural movement that adapts in real-time to user behavior.
By 2030, biomechanical prosthetic limbs will be fully integrated with the nervous system, allowing users to control movement effortlessly, feel textures through sensory feedback, and experience mobility that closely resembles natural limb function. These advancements will redefine independence for amputees, making prosthetic limbs feel like a true extension of the body.
2. Smart Materials: Making Prosthetics More Flexible and Durable
One of the biggest challenges in prosthetic design has been finding materials that are both strong and lightweight. Traditional materials like metal and rigid plastics provided durability but often caused discomfort, weight imbalance, and limited flexibility. Biomechanical engineering is solving this with smart materials that adapt to the user’s movements.
New developments in shape-memory alloys, carbon fiber composites, and biopolymer gels are allowing prosthetic limbs to bend, flex, and adjust to movement in real-time. These materials are designed to respond to pressure and temperature changes, making them more comfortable for long-term wear. Some of these smart materials even have self-healing properties, meaning small cracks or damages can repair themselves, reducing the need for frequent replacements.
By 2030, prosthetic limbs will be made from ultra-lightweight, flexible materials that adjust to each user’s unique biomechanics, ensuring long-lasting durability, comfort, and superior performance. This will not only improve mobility but also enhance the overall experience of prosthetic wearers, making artificial limbs more adaptable to different environments and activities.
3. AI-Driven Motion Analysis: Making Prosthetic Movements More Natural
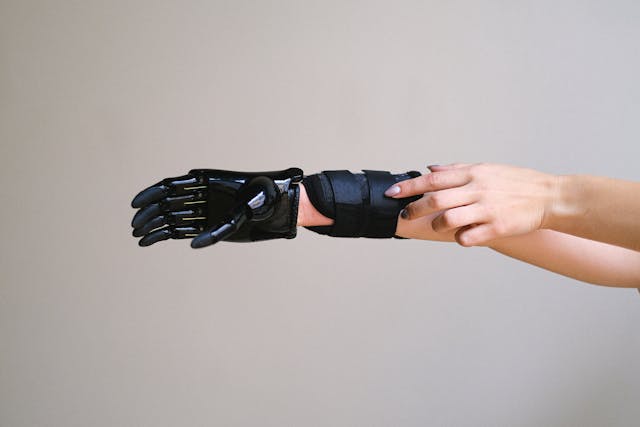
A major breakthrough in biomechanical prosthetics is AI-driven motion analysis, which allows prosthetic limbs to learn from user behavior and adapt movement accordingly. Unlike older prosthetics that relied on fixed settings, AI-powered prosthetics can continuously adjust their movements to match the user’s needs.
Through real-time gait analysis and motion tracking, AI algorithms study how a user walks, runs, or performs daily activities. If the user struggles with balance or uneven terrain, the AI will automatically adjust joint flexibility, foot positioning, and shock absorption, ensuring a smooth and stable experience. Over time, the prosthetic becomes smarter, adapting to changes in weight distribution, muscle fatigue, and terrain challenges.
By 2030, AI-driven prosthetic limbs will function just like biological limbs, allowing for fluid, intuitive movement without the need for constant manual adjustments. This will make prosthetic usage more natural, reducing strain on the body and improving overall user confidence.
4. Neural Interfaces: Direct Brain Control for Prosthetic Limbs
One of the most exciting areas of biomechanical engineering is neural integration, where prosthetic limbs are directly connected to the brain and nervous system. This allows users to control movement just by thinking about it, without relying on external switches or muscle signals.
Through brain-machine interfaces (BMIs) and peripheral nerve stimulation, neural interfaces capture electrical signals from the brain, translating them into movement commands for the prosthetic limb. This means that an amputee using a brain-controlled prosthetic arm can pick up a glass or type on a keyboard just by imagining the movement.
By 2030, neural-controlled prosthetic limbs will become mainstream, enabling seamless, thought-driven mobility. Combined with AI-powered learning, these prosthetics will continuously improve over time, making movement more intuitive and reducing the mental effort required to operate them.
5. Haptic Feedback: Restoring the Sense of Touch
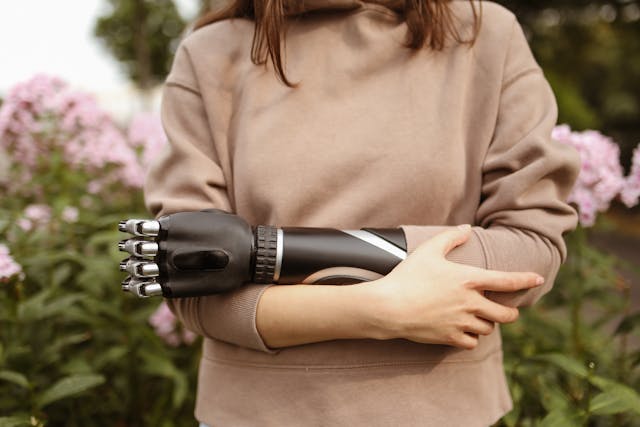
For decades, prosthetic limbs focused only on restoring movement, but without the sense of touch, even the most advanced prosthetic limbs still feel artificial. Haptic feedback technology is changing this by allowing users to feel textures, pressure, and temperature through their artificial limbs.
Using pressure sensors, electro-tactile stimulation, and AI-driven sensory mapping, haptic prosthetics recreate the sensation of touch and grip force. When a user picks up an object, their prosthetic hand detects its weight, texture, and firmness, sending signals to their brain through electrical nerve stimulation.
By 2030, prosthetic limbs will provide full sensory restoration, allowing users to distinguish between soft and hard surfaces, feel temperature variations, and experience real-time touch feedback. This advancement will dramatically improve user confidence and overall quality of life, making prosthetic limbs feel truly natural.
6. The Future of Biomechanical Prosthetics: What to Expect by 2030
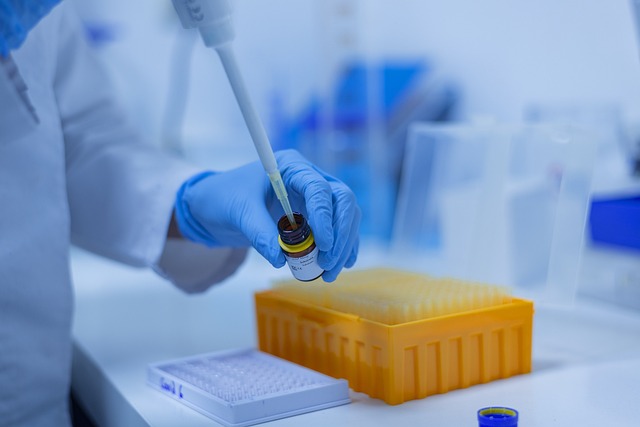
With rapid advancements in biomechanical engineering, AI, and neural interfaces, the next generation of prosthetic limbs will be more advanced, intuitive, and responsive than ever before. By 2030, we can expect prosthetics to feature:
- Seamless brain integration, allowing full thought-controlled movement.
- Haptic feedback that restores touch, texture, and temperature sensation.
- Ultra-lightweight smart materials that adjust to real-time movement and self-repair minor damage.
- AI-driven motion analysis that learns and improves prosthetic performance over time.
These innovations will make prosthetic limbs virtually indistinguishable from biological ones, ensuring that amputees experience unparalleled mobility, independence, and confidence.
7. The Role of Soft Robotics in Creating More Natural Movements
Soft robotics is revolutionizing the way prosthetic limbs function by introducing flexible, muscle-like materials that mimic human motion. Unlike traditional rigid prosthetics that rely on mechanical joints and motors, soft robotic prosthetics use air pressure, hydraulics, and bio-inspired materials to create smoother, more organic movements.
By incorporating pneumatic actuators and artificial tendons, these prosthetics can bend, stretch, and flex naturally, closely resembling the movement of real muscles. This eliminates the jerky, robotic motion that many artificial limbs previously exhibited, making movement feel more fluid and effortless. Additionally, soft robotic designs reduce the strain on the residual limb, improving long-term comfort and wearability.
By 2030, soft robotics will allow prosthetic users to experience greater dexterity, better range of motion, and improved energy efficiency. This will be particularly beneficial for lower-limb prosthetic users, as robotic feet and ankles will be able to adjust dynamically to different walking surfaces, reducing the risk of falls and fatigue.
8. Energy-Efficient Prosthetic Designs for Longer Use
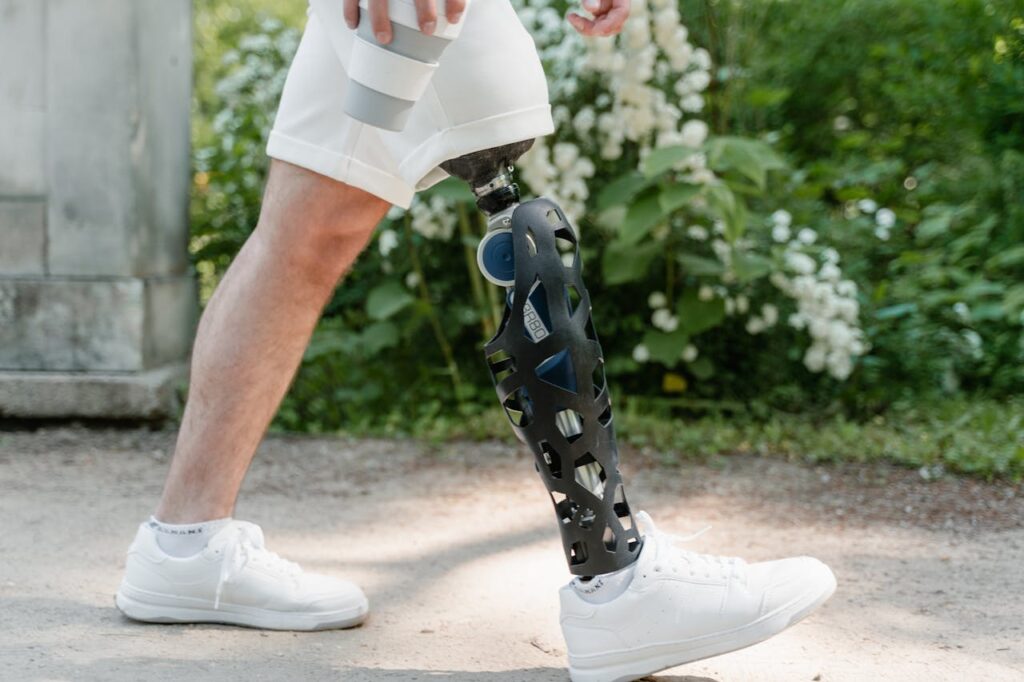
One of the ongoing challenges in prosthetic technology is energy consumption, particularly for bionic limbs that rely on battery power to function. Many high-tech prosthetics today require frequent recharging, limiting their usability for extended periods. Biomechanical engineering is now focusing on energy-efficient solutions that maximize battery life while maintaining optimal performance.
New developments in energy harvesting technology are making it possible for prosthetic limbs to generate their own power. Some prosthetics now integrate piezoelectric materials that convert movement into electrical energy, effectively allowing the limb to self-charge as the user walks or moves their fingers. Additionally, advanced battery technology, including solid-state and graphene-based batteries, is making prosthetic limbs last significantly longer on a single charge.
By 2030, prosthetic users will experience significantly extended battery life and self-sustaining energy sources, reducing the inconvenience of frequent recharging. This will ensure that high-performance bionic limbs remain operational for longer hours without interruptions, making them more reliable in daily life.
9. Personalized Prosthetic Skins for a More Natural Look and Feel
A major aspect of prosthetic design that has historically been overlooked is aesthetics and personalization. Many prosthetic users want their artificial limbs to feel like an extension of their identity, not just a functional replacement. Advances in biomechanical engineering are now enabling customized prosthetic skins that mimic the look, feel, and even temperature of human skin.
Modern prosthetic coverings are now made from silicone-based bio-synthetic materials that match individual skin tones, textures, and even subtle details like veins and freckles. Some prosthetic skins also feature embedded heating elements, allowing them to match the temperature of the user’s body, preventing the artificial limb from feeling unnaturally cold.
By 2030, prosthetic users will have access to fully customizable, life-like prosthetic skins, ensuring that their artificial limbs not only function well but also feel and appear natural. This will improve social confidence, emotional well-being, and overall acceptance of prosthetic limbs as everyday extensions of the human body.
10. How Prosthetics Are Becoming More Intuitive Through Machine Learning
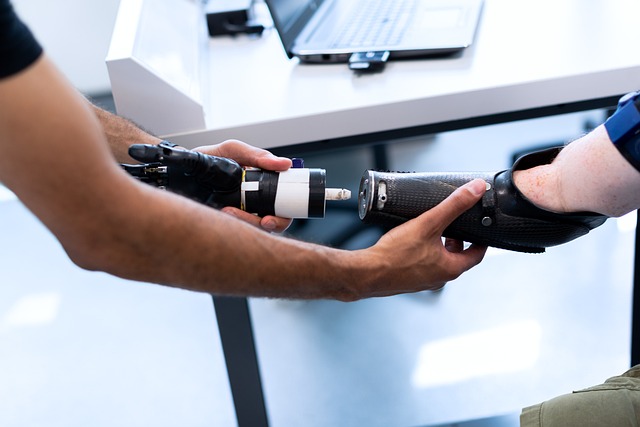
Prosthetic limbs are becoming increasingly intelligent, thanks to machine learning algorithms that analyze user movement and automatically adjust performance. Unlike older prosthetics that required manual recalibration, modern bionic limbs use adaptive AI systems to fine-tune their responsiveness based on real-world use.
By collecting data on walking patterns, hand movements, and grip strength, machine learning prosthetics can predict user intent and make adjustments before the user even realizes they need them. This means that if a person frequently shifts between walking and running, their prosthetic leg can automatically modify resistance levels and balance control in real time. Similarly, an advanced bionic hand can fine-tune grip pressure based on the shape and weight of an object, ensuring better control without accidental drops.
By 2030, machine learning will make prosthetic limbs smarter and more intuitive, allowing them to anticipate the user’s needs with minimal conscious effort. This will help bridge the gap between artificial and biological limb function, making movement feel truly natural.
11. The Impact of Cloud-Connected Prosthetics on Remote Adjustments
As prosthetic technology advances, cloud connectivity is emerging as a game-changing feature, allowing for real-time updates, remote diagnostics, and software enhancements. Users no longer need to visit clinics frequently for adjustments, as cloud-based prosthetic systems can automatically receive improvements and optimizations through wireless networks.
Cloud-connected prosthetic limbs allow users to customize their movement settings via smartphone apps, adjusting sensitivity, grip strength, and walking mechanics instantly. Additionally, prosthetists can monitor performance remotely and make necessary changes without requiring an in-person visit, reducing downtime and improving user convenience.
By 2030, cloud connectivity will make prosthetic maintenance easier than ever, ensuring that users always have access to the latest updates, improved AI algorithms, and faster troubleshooting solutions. This will lead to a more seamless, efficient experience for prosthetic users, eliminating many of the common frustrations associated with traditional artificial limbs.
12. Biomechanical Prosthetics in Sports and High-Performance Activities
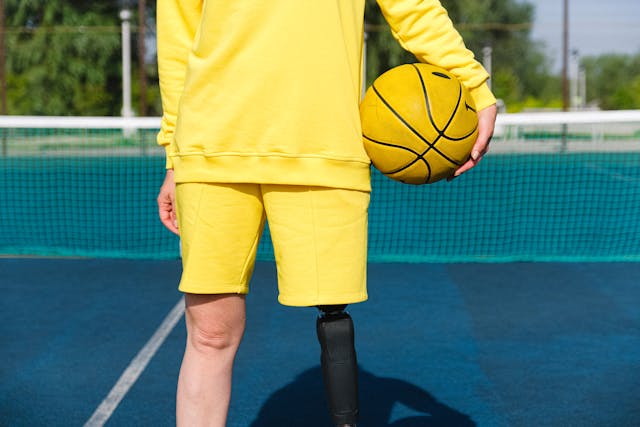
Biomechanical engineering is also transforming sports prosthetics, allowing amputees to compete at elite levels with cutting-edge bionic limbs. Advanced materials, AI-powered motion control, and energy-efficient actuators are enabling athletes to run, jump, and perform explosive movements with greater efficiency than ever before.
Unlike older sports prosthetics that focused purely on basic speed and strength, new designs incorporate real-time motion tracking, shock absorption, and force redistribution, allowing athletes to perform at optimal levels while minimizing the risk of injury. Additionally, adjustable resistance settings let users fine-tune their prosthetics for different types of sports, from sprinting to weightlifting.
By 2030, bionic sports prosthetics will be more powerful, dynamic, and tailored to specific athletic needs, helping athletes push their limits without worrying about technological constraints. This will redefine inclusivity in professional sports, ensuring that prosthetic users have access to the same level of competition as their able-bodied counterparts.
Final Thoughts: The Future of Biomechanical Prosthetics Is Here
Biomechanical engineering is redefining prosthetic design, transforming artificial limbs from static replacements into intelligent, highly adaptable systems. The combination of AI-driven motion learning, soft robotics, neural interfaces, and advanced materials is ensuring that prosthetic limbs not only restore function but enhance the way users interact with the world.
By 2030, prosthetic users will experience greater mobility, seamless control, and even restored sensation, making artificial limbs feel as natural as biological ones. These advancements will remove barriers, improve accessibility, and empower amputees to live more active, independent lives.
At Robobionics, we are committed to leading the next wave of biomechanical prosthetic innovation, ensuring that users experience cutting-edge technology that is both practical and life-changing. If you are ready to explore the future of high-performance, AI-powered prosthetics, book a free demo with Robobionics today and take the next step toward a world where mobility knows no limits.